The Only Guide to Alcast Company
The Only Guide to Alcast Company
Blog Article
Excitement About Alcast Company
Table of ContentsSome Ideas on Alcast Company You Should KnowThe Best Strategy To Use For Alcast CompanyAlcast Company for DummiesThe Of Alcast CompanyThe Facts About Alcast Company Revealed9 Easy Facts About Alcast Company ExplainedThe Definitive Guide for Alcast CompanyAlcast Company Fundamentals Explained
It possessed excellent stamina and machinability. There are lots of various other light weight aluminum alloys that can be used for casting parts. To learn which alloys would benefit your tasks, call Impro.

Different components and amounts create a wide range of preferable physical and chemical homes. And the Aluminum Association (AA), based in The United States and copyright, has developed specifications that control light weight aluminum alloys' structure, homes, and nomenclature. There are two kinds of light weight aluminum alloys functioned and cast. Shop employees create these alloy kinds in different methods, which substantially impacts their qualities.
Not known Incorrect Statements About Alcast Company
Cast aluminum alloys are made by melting pure light weight aluminum and combining it with other steels while in fluid kind. After that the mix is put right into a sand, die, or investment mold. After solidification, the steel is removed from its mold and mildew. At this phase, it remains in either its final type or as a billet or ingot for additional processing.
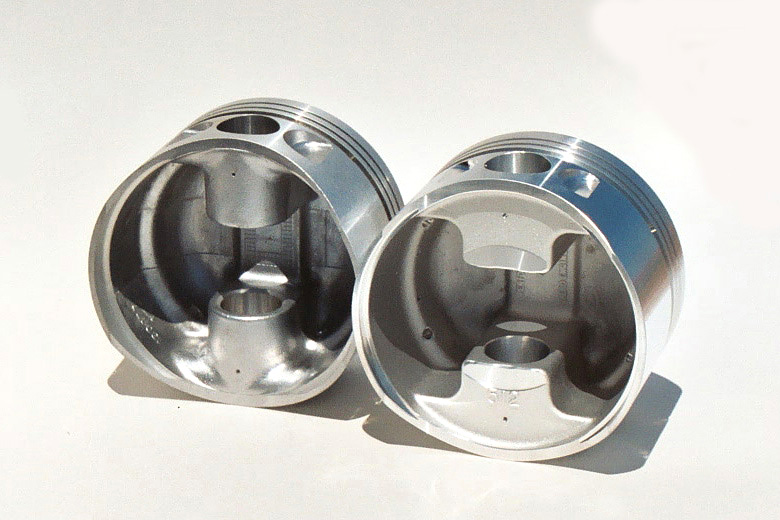
There are several small distinctions between functioned and cast light weight aluminum alloys, such as that cast alloys can contain extra significant amounts of various other steels than wrought alloys. The most remarkable difference between these alloys is the construction procedure with which they will certainly go to provide the final item. Apart from some surface treatments, cast alloys will exit their mold and mildew in virtually the specific solid form preferred, whereas wrought alloys will certainly undergo numerous adjustments while in their solid state
Not known Details About Alcast Company
If you assume that a wrought alloy might be the most effective for your task, take a look at a few of our short articles that clarify more concerning details wrought alloys, such as Alloy 6061 and Alloy 6063. On the various other hand, if you assume an actors alloy would certainly be much better for you, you can discover more concerning some cast alloys in our Alloy 380 and Alloy 383 posts (coming soon).
When selecting an aluminum foundry for your manufacturing demands, it's crucial to examine a number of aspects. Among one of the most crucial facets to think about is the experience and competence of the shop. Picking a foundry who has the best expertise of the aluminum casting procedure, and the portfolio to show for it, helps to have a successful end result for your task.
A Biased View of Alcast Company
Having the experience and sector understanding to craft your castings for optimum manufacturing and quality outcomes will enhance the task. Producing aluminum castings needs a complicated set of procedures to accomplish the ideal outcomes. When making a decision on a brand-new light weight aluminum foundry to companion with, guarantee they have substantial industry experience and are knowledgeable regarding all facets of the aluminum spreading process: layout, manufacturing, material analysis, and item testing.
The factory must also have a tried and tested record of delivering outstanding items that fulfill or exceed consumer expectations. Quality control ought to likewise be at the top of your listing when selecting a light weight aluminum factory. By collaborating with a certified foundry who follows the requirements for top quality control, you can protect the honesty of your product and ensure it fulfills your specs.
Alcast Company Fundamentals Explained
By choosing a business who provides solutions that satisfy or surpass your item needs, you can be sure that your task will certainly be finished with the utmost precision and efficiency. Various components require various manufacturing strategies to cast light weight aluminum, such as sand spreading or die spreading.
Pass away casting is the name given to the procedure of creating intricate metal parts through use mold and mildews of the part, also referred to as dies. The process makes use of non-ferrous metals which do not consist of iron, such as light weight aluminum, zinc and magnesium, as a result of the preferable properties of the metals such as low weight, higher conductivity, non-magnetic conductivity and resistance to corrosion.
Pass away casting production is fast, making high production degrees of parts easy. It produces even more components than any type of various other procedure, with a high level of accuracy and repeatability. To discover more regarding die spreading and die spreading materials made use of while doing so, reviewed on. There are 3 sub-processes that fall under the category of die casting: gravity pass away spreading (or permanent mold casting), low-pressure die casting and high-pressure die casting.
Indicators on Alcast Company You Should Know
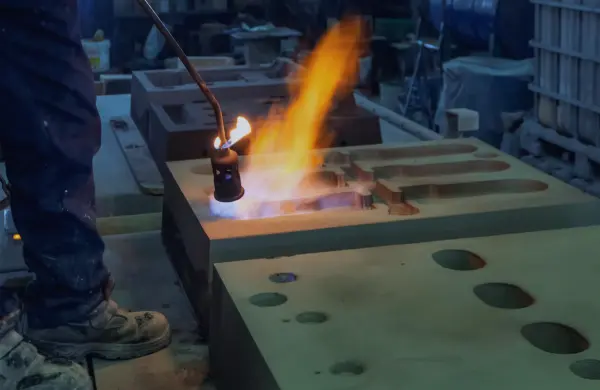
The pure metal, also called ingot, is included in the heater and maintained the molten temperature of the steel, which is then transferred to the shot chamber and injected into the die. The stress is then kept as the metal strengthens. Once the steel blog here solidifies, the cooling process begins.
The thicker the wall surface of the part, the longer the cooling time as a result of the quantity of interior steel that also needs to cool. After the element is completely cooled down, the die halves open and an ejection device pushes the component out. Adhering to the ejection, the die is shut for the next injection cycle.
The Alcast Company Ideas
The flash is the additional material that is cast throughout the procedure. Deburring eliminates the smaller sized pieces, called burrs, after the cutting process.
Today, top producers make use of x-ray screening to see the whole inside of elements without reducing into them. To obtain to the ended up product, there are 3 primary alloys utilized as die casting material to pick from: zinc, light weight aluminum and magnesium.
Zinc is one of the most pre-owned alloys for die casting due to its reduced price of raw materials. Its deterioration resistance also allows the elements to be long lasting, and it is one of the much more castable alloys due to its lower melting factor.
Unknown Facts About Alcast Company
As pointed out, this alloy is just one of one of the most typically used, yet manufactures will, at times, choose light weight aluminum over zinc due to aluminum's manufacturing benefits. Aluminum is very affordable and one of the extra versatile alloys. Light weight aluminum is used for a number of different products and markets anything from window frames to aerospace materials.
Report this page